Nowdays, under the background of the rapid development of new energy vehicles and energy storage industry, the capacity of lithium batteries has been accelerated, and lithium batteries have entered the era of mass manufacturing. However, it is worth noting that, on the one hand, peak carbon dioxide emissions and carbon neutrality have become trends and requirements; On the other hand, large-scale lithium battery manufacturing, cost reduction and economic pressure are increasingly prominent.
The focus of lithium battery industry: consistency, safety and economy of batteries. The temperature and humidity and cleanliness in the dryroom will seriously affect the consistency of the battery; At the same time, the speed control and moisture content in the dryroom will seriously affect the performance and safety of the battery; The cleanliness of the drying system, especially the metal powder, will also seriously affect the performance and safety of the battery.
And the energy consumption of the drying system will seriously affect the economy of the battery, because the energy consumption of the whole drying system has accounted for 30% to 45% of the whole lithium battery production line, so whether the energy consumption of the whole drying system can be controlled well will actually affect the cost of the battery.
To sum up, it can be seen that the intelligent drying of lithium battery manufacturing space mainly provides a dry, clean and constant temperature protection environment for lithium battery production line. Therefore, the advantages and disadvantages of intelligent drying system can not be underestimated on the guarantee of battery consistency, safety and economy.
In addition, as the largest export market of China's lithium battery industry, the European Commission has adopted a new battery regulation: from July 1, 2024, only power batteries with a carbon footprint statement can be put on the market. Therefore, it is urgent for China lithium battery enterprises to accelerate the establishment of a low-energy, low-carbon and economical battery production environment.
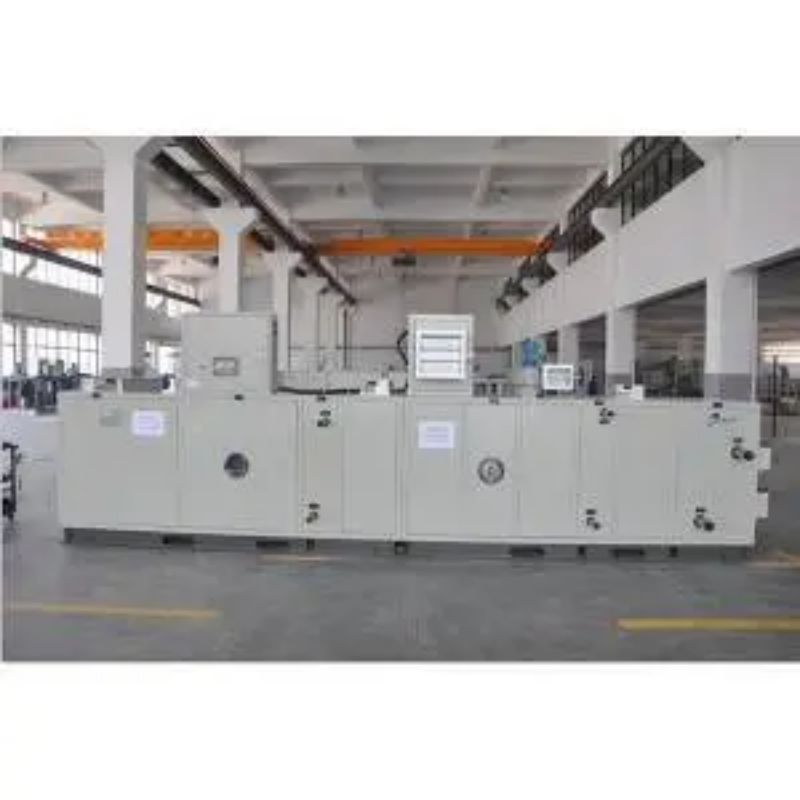
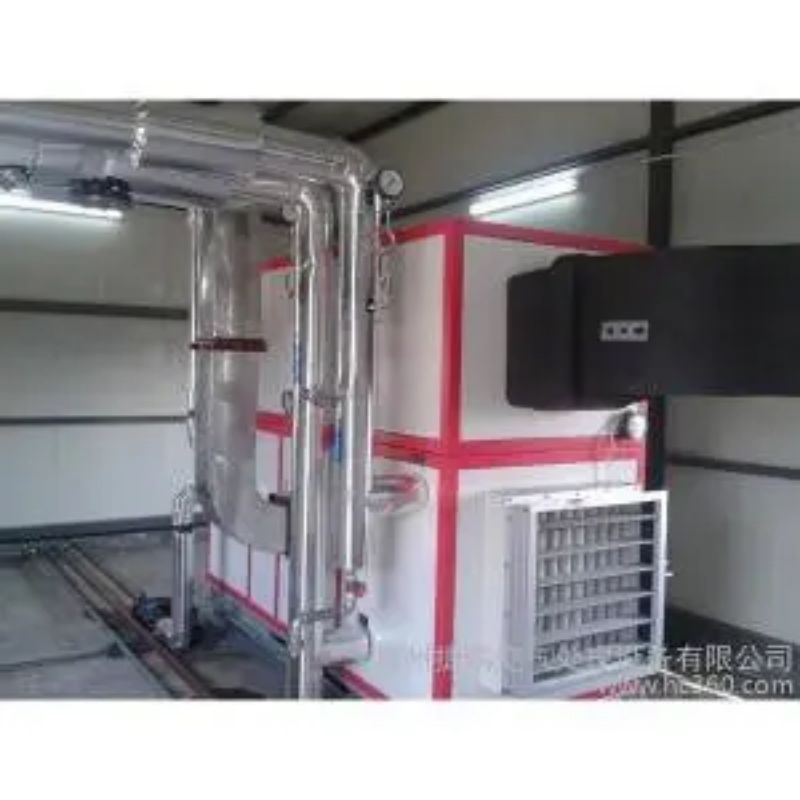
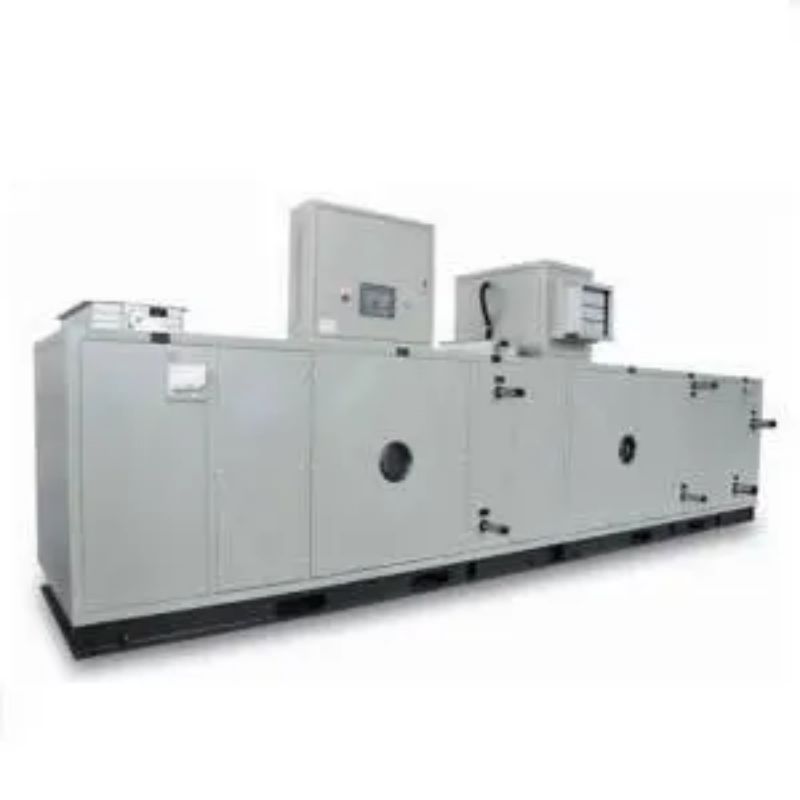
There are four main directions to reduce the energy consumption of the whole lithium battery production environment:
First, constant indoor temperature and humidity to reduce energy consumption. In the past few years, HZDryair has been doing dew point feedback control in the room. The traditional concept is that the lower the dew point in the drying room, the better, but the lower the dew point, the greater the energy consumption. "Keep the required dew point constant, which can greatly reduce energy consumption under various preconditions."
Second, control the air leakage and resistance of the drying system to reduce energy consumption. The energy consumption of dehumidification system has a great influence on the added fresh air volume. How to improve the airtightness of the air duct, unit and drying room of the whole system, so as to reduce the addition of fresh air volume has become the key. "For every 1% reduction of air leakage, the whole unit can save 5% of operating energy consumption. At the same time, cleaning the filter and surface cooler in time in the whole system can reduce the resistance of the system and thus reduce the operating power of the fan. "
Third, waste heat is used to reduce energy consumption. If waste heat is used, the energy consumption of the whole machine can be reduced by 80%.
Fourth, use special adsorption runner and heat pump to reduce energy consumption. HZDryair takes the lead in introducing 55℃ low temperature regeneration unit. By modifying the hygroscopic material of the rotor, optimizing the runner structure, and adopting the most advanced low-temperature regeneration technology in the industry at present, low-temperature regeneration can be realized. The waste heat can be steam condensation heat, and the hot water at 60℃~70℃ can be used for unit regeneration without consuming electricity or steam.
In addition, HZDryair has developed 80℃ medium temperature regeneration technology and 120℃ high temperature heat pump technology.
Among them, the dew point of the low dew point rotary dehumidifier unit with high temperature air inlet at 45℃ can reach ≤-60℃. In this way, the cooling capacity consumed by surface cooling in the unit is basically zero, and the heat after heating is also very small. Taking a 40000CMH unit as an example, the annual energy consumption of a unit can save about 3 million yuan and 810 tons of carbon.
Hangzhou Dryair Air Treatment Equipment Co., Ltd., established after the second restructuring of Zhejiang Paper Research Institute in 2004, is an enterprise specializing in the research, development and production of dehumidification technology for filter rotors, and is also a national high-tech enterprise.
Through cooperation with Zhejiang University, the company adopts the dehumidification runner technology of NICHIAS in Japan/PROFLUTE in Sweden to conduct professional research, development, production and sales of various types of runner dehumidification systems; A series of environmental protection equipment developed by the company have been widely and maturely applied in many industries.
In terms of production capacity, the company's current production capacity of dehumidifiers has reached more than 4,000 sets.
In terms of customers, customer groups are all over the world, among which the leading customers in representative and focused industries: lithium battery industry, biomedical industry and food industry all have cooperation. In terms of lithium battery, it has established in-depth cooperative relations with ATL/CATL, EVE, Farasis, Guoxuan, BYD, SVOLT, JEVE and SUNWODA.
Post time: Sep-26-2023